PROCESSING APPLICATION
Hold tight! We’re comparing your resume to the job requirements…
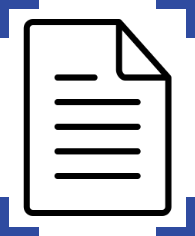
ARE YOU SURE YOU WANT TO APPLY TO THIS JOB?
Based on your Resume, it doesn't look like you meet the requirements from the employer. You can still apply if you think you’re a fit.
Job Requirements of Manufacturing Engineer:
-
Employment Type:
Full-Time
-
Location:
Knoxville, TN (Onsite)
Do you meet the requirements for this job?
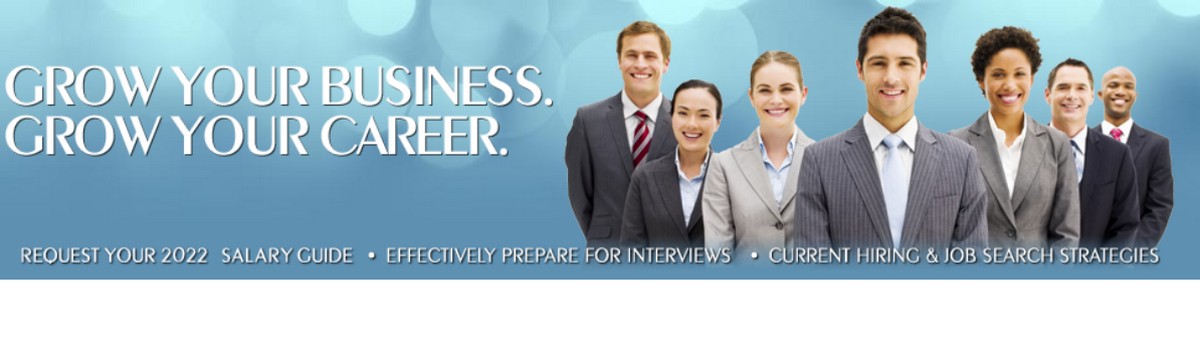
Manufacturing Engineer
Travel:
Significant travel (50%) to New England will be required during the first six months. Ongoing periodic travel will also be expected.
Role Overview:
The Manufacturing Engineer will be responsible for designing and implementing efficient, cost-effective manufacturing processes that meet product specifications and quality standards. This role involves recommending and executing process improvements, supporting production optimization, and coordinating the launch of new or updated products. Core responsibilities include process enhancement, problem-solving, project management, and employee training.
Primary Responsibilities:
- Research, design, and develop manufacturing processes, including production workflows, assembly methods, and equipment.
- Analyze and interpret complex part drawings to ensure alignment with design intent.
- Coordinate the launch of new or revised products by setting goals, training staff, and evaluating outcomes.
- Utilize project management techniques to define, document, and implement tools, gauges, fixtures, equipment, routings, and CMM/CNC programs.
- Design, develop, test, or source tools, machinery, and equipment to support manufacturing processes.
- Perform product and process analysis to drive cost reduction, quality improvements, and efficiency gains.
- Manage and maintain the accuracy of the manufacturing routing database, including operation sequences, labor hours, setup and changeover times, and machine cycle times.
- Work with external technical support and provide continuous training for internal teams.
- Represent manufacturing in cross-functional teams.
- Work effectively within a team environment while independently prioritizing tasks and meeting deadlines.
- Perform additional duties as assigned.
Note: This list outlines the primary responsibilities and is not comprehensive. Duties may evolve based on business needs.
Education & Experience:
- Bachelor’s degree in Mechanical Engineering (BSME) or equivalent.
- Minimum of 5 years of experience in a manufacturing environment, preferably within a similar industry.
- Strong understanding of lean manufacturing principles.
- Proven ability to address shop floor needs and concerns effectively.
- Outstanding customer service and interpersonal skills.
Key Skills & Competencies:
- Strong command of the English language (written and verbal).
- Proficiency in Microsoft Word, Excel, Access, and PowerPoint.
- Familiarity with SolidWorks and/or CAM is a plus.
- Knowledge of CMM programming and PC-DMIS is advantageous.
Training Requirements:
- Complete all training as required by the role and department.
- Actively participate in company initiatives and improvement projects (e.g., Kaizen events, 5S).
Physical Demands:
- Must be able to sit, stand, walk, climb, bend, stoop, push, pull, carry, and twist.
- Ability to lift up to 50 pounds.
- Note: Reasonable accommodations can be made for individuals with disabilities to perform essential duties.
Work Environment & Personal Protective Equipment:
Employees may encounter:
- Manufacturing noise, airborne chemicals, fine particulate dust, varying temperatures, and industrial lighting.
- Potential exposure to excessive noise, vibrations, moving machinery, confined spaces, high temperatures, odors, dust, and chemical hazards.
Personal Protective Equipment (PPE):
- Safety glasses with side shields and hearing protection are mandatory on the manufacturing floor.
- Additional PPE, such as safety footwear or task-specific gear, may be required based on the department or job task.
Benefits Overview:
- Health, dental, and vision insurance.
- Prescription drug coverage.
- Employee assistance program.
- Group life and disability insurance.
- 401(k) plan with profit-sharing options.
- Employee stock purchase program at a discount.
- Paid time off, holidays, and winter shutdown.
- Tuition assistance program.
- Discounts on company products.
- Service awards.